تزریق پلاستیک
در این بخش ما ویژگی ها و خصوصیات پایه ای تکنولوژی تزریق پلاستیک را بررسی می کنیم. با مطالعه ی این بخش از مدرسه پرینت سه بعدی می توانید اطلاعاتی از مکانیک تکنولوژی تزریق پلاستیک با پرینت سه بعدی ، ویژگی های مثبت و محدودیت های آن کسب کنید.
تزریق پلاستیک یک تکنولوژی ساخت برای تولید انبوه قطعات پلاستیکی یکسان با خطای پایین است. در تزریق پلاستیک ابتدا گرانول های پلیمر ذوب می شوند و سپس تحت فشار به درون یک قالب تزریق می شوند. پلاستیک مایع درون قالب خنک شده و جامد می شود. مواد اولیه تزریق پلاستیک پلیمرهای ترموپلاستیکی هستند که قابلیت رنگ آمیزی و پر شدن توسط افزودنی های دیگر را دارند.
تقریبا همه قطعات پلاستیکی که به طور روزمره از آنها استفاده می کنیم با استفاده از تکنولوژی تزریق پلاستیک ساخته شده اند: از قطعات خودرو و محفظه دستگاه های الکترونیکی گرفته تا لوازم آشپزخانه.
دلیل محبوبیت و استفاده گسترده از تزریق پلاستیک، هزینه بسیار پایین ساخت هر قطعه در تیراژهای بالا است. تزریق پلاستیک تکرار پذیری بالا را در کنار آزادی بالای طراحی ارایه می کند. محدودیت های اصلی تزریق پلاستیک از نوع اقتصادی هستند چون با اینکه تولید با استفاده از تزریق پلاستیک در تیراژ بالا بسیار به صرفه است، اما در مقابل سرمایه اولیه به نسبت بالایی برای شروع پروسه لازم است. از دیگر محدودیت های تزریق پلاستیک زمان نسبتا بالای رسیدن از طرح به تولید قطعه است(حداقل ۴ هفته).
در این مقاله در ابتدا می بینیم قطعات تزریق پلاستیک چگونه ساخته می شوند و تکنولوژی تزریق پلاستیک چگونه کار می کند. همچنین ویژگی های کلی این پروسه را که روی طراحی یک قطعه برای تزریق پلاستیک تاثیر دارند بررسی می کنیم. در ادامه به طور دقیق تر به مکانیک تکنولوژی تزریق پلاستیک وارد می شویم ، تاثیر این طرز کار روی هزینه های ساخت با این تکنولوژی را بررسی می کنیم و قابلیت های و محدودیت های کلیدی آن را بر می شماریم.
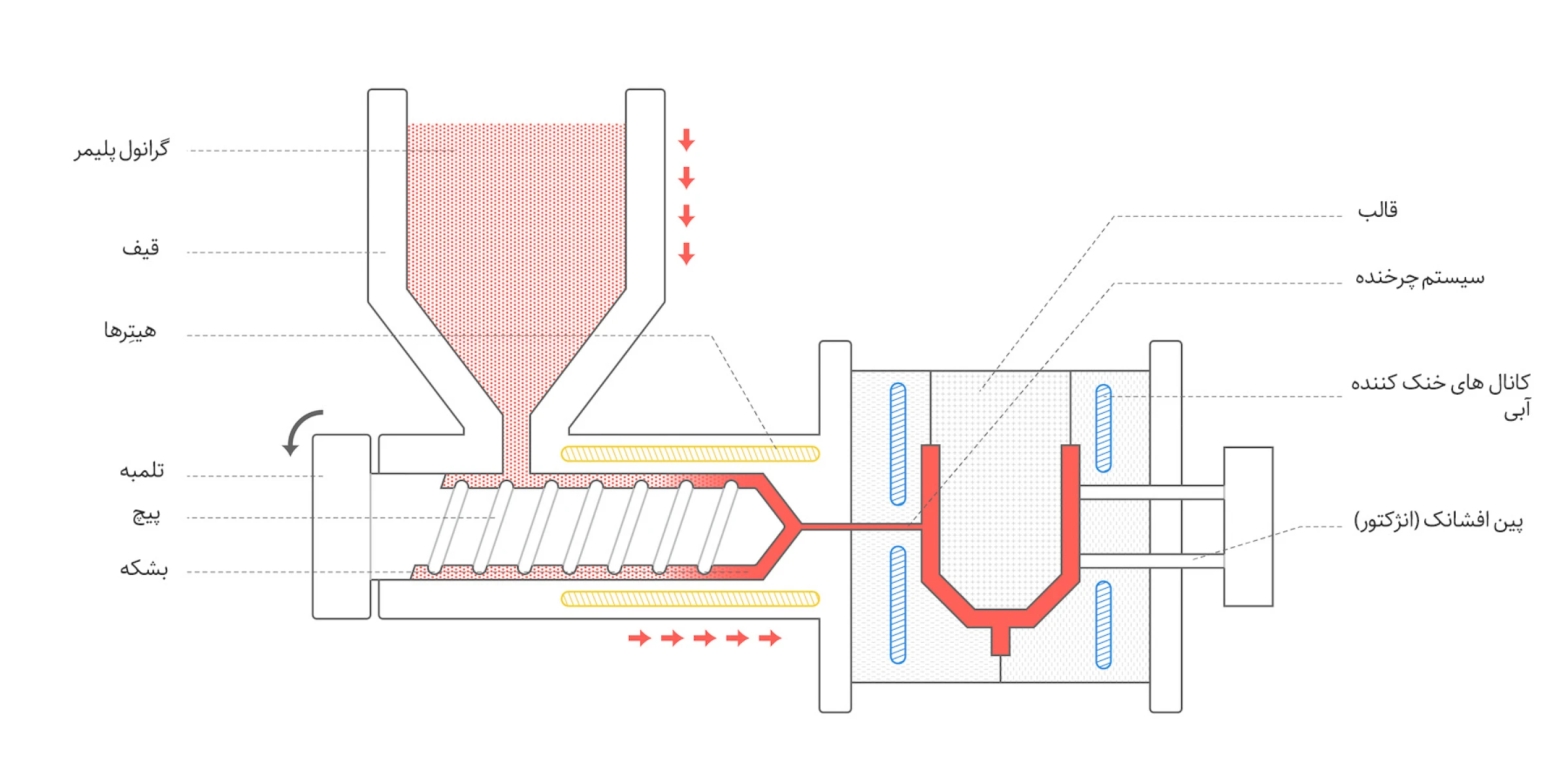
شیوه کار یک سیستم معمول تزریق پلاستیک
طرز کار تزریق پلاستیک:
۱.ابتدا گرانول های پلیمر خشک شده و در قیف قرار داده می شوند. این گرانول ها در قیف با پودرها و پیگمنت های رنگی و دیگر افزودنی های تقویت کننده ترکیب می شوند.
۲.گرانول ها به بشکه تغذیه می شوند. گرانول ها در بشکه حرارت دیده،با یکدیگر ترکیب شده و با یک پیچ چرخان به سمت قالب هدایت می شوند. هندسه پیچ و بشکه به گونه ای بهینه طراحی شده است که به بالا بردن فشار به میزان لازم و ذوب شدن ماده کمک کند.
۳.تلمبه به جلو حرکت کرده و پلاستیک ذوب شده از طریق سیستم چرخنده به قالب تزریق می شود و همه فضای خالی قالب را پر می کند. با پایین آمدن دمای ترموپلاستیک، ماده جامد شده و شکل قالب را به خود می گیرد.
- در نهایت قالب گشوده شده و قطعه جامد توسط پین های افشانک به بیرون هل داده می شود، سپس قالب دوباره بسته شده و پروسه برای تزریق قطعه بعدی تکرار می شود.
تکرار این پروسه می تواند بسیار سریع انجام شود: چرخه تزریق پلاستیک معمولا بسته به اندازه قطعه می تواند از ۳۰ تا ۹۰ ثانیه طول بکشد.
پس از آماده شدن محصول، قطعه روی کانوایر و یا در یک مخزن نگهدارنده رها می شود. معمولا قطعاتی که با تزریق پلاستیک ساخته می شوند به محض ساخت آماده استفاده بوده و نیازی به طی مراحل پولیش ، پرداخت و پست پروسس ندارند.
ساخت قالب تزریق پلاستیک
یک قالب مثل تصویر نگاتیو یک عکس است: هندسه و الگوی سطح قالب به طور مستقیم روی شکل قطعه تزریق پلاستیک شده تاثیر می گذارد.
معمولا بیشتر هزینه اولیه صرف ساخت قالب تزریق پلاستیک می شود: ساخت یک قالب معمول از حدود ۲۰۰۰-۵۰۰۰دلار برای قالب های ساده و تیراژ های نسبتا پایین (بین ۱۰۰۰ تا ۱۰۰۰۰) شروع شده و می تواند برای قالب های تیراژ بالا تا ۱۰۰هزاردلار بالا رود.(۱۰۰هزار قطعه یا بیشتر).
این هزینه به خاطر تخصص بالایی است که برای ساخت یک قالب باکیفیت لازم است.قالبی که بتواند به طور دقیق هزاران(یا صدها هزار) قطعه را تولید کند.
قالب های تزریق پلاستیک معمولا با ماشین CNC از آلومینیوم یا استیل ساخته می شوند و سپس تا استانداردهای بالا پولیش، پرداخت و پست پروسس می شوند. به جز نگاتیو قطعه، قالب های تزریق پلاستیک قابلیت هایی مثل سیستم تزریق ، کانال های داخلی خنک کننده با آب و… را که به سرعت پروسه کمک می کنند در خود جای می دهند.
پیشرفت های اخیر در مواد اولیه پرینت سه بعدی، امکان ساخت قالب تزریق پلاستیک با پرینت سه بعدی را فراهم کرده است.
قالب های تزریق پلاستیک پرینت سه بعدی ، بسیار ارزان تر از قالب های معمول هستند اما تنها برای تزریق پلاستیک در تیراژ پایین( کمتر از ۱۰۰ قطعه) کاربرد دارند.
تولید در این تیراژهای پایین در گذشته بدون استفاده از پرینت سه بعدی در تزریق پلاستیک امکان پذیر نبود چرا که هزینه ساخت قالب با روش های سنتی بسیار بالاست و محصول نهایی نمی تواند به صرفه به بازار ارایه شود.
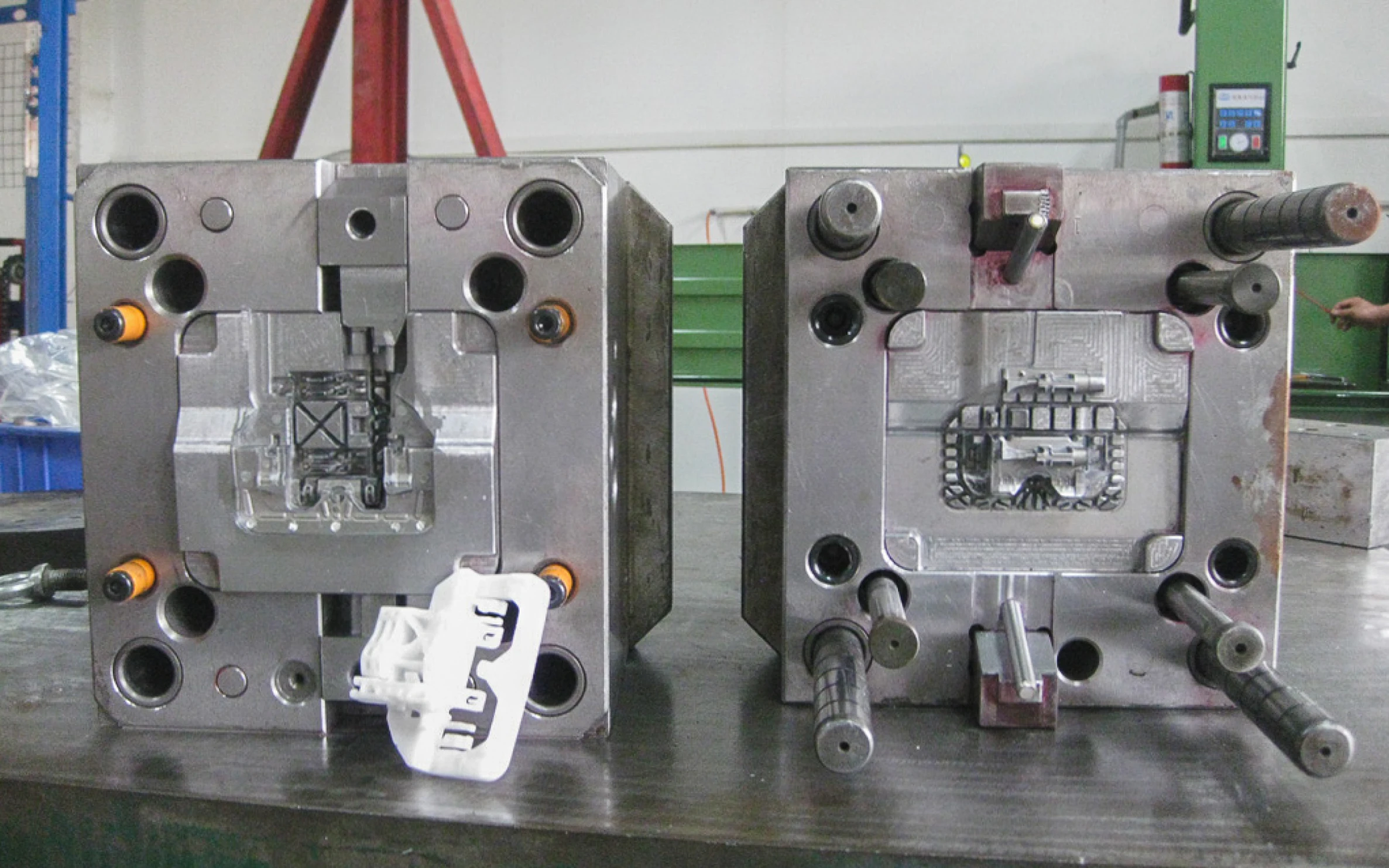
یک قالب صنعتی برای تولید ده ها هزار قطعه پلاستیکی. قالب سمت راست هسته قالب سمت چپ را تشکیل می دهد. (تصویر متعلق به شرکت Promolding است.)
آناتومی یک قالب تزریق پلاستیک
ساده ترین قالب تزریق پلاستیک، قالب Straight-pull است. این قالب از دو نیمه تشکیل شده است: قسمت Cavity یا حفره و Core یا هسته.
این قالب ها پر استفاده ترین قالب ها در تزریق پلاستیک هستند. طراحی و ساخت آنها آسان است که کل هزینه را به نسبت پایین می آورد. در مقابل طراحی این قالب ها با محدودیت مواجه است: قطعه حتما باید روی هر طرف هندسه دوبعدی داشته و بیرون زدگی نداشته باشد(حجم هایی که از زیر ساپورت نمی شوند.).
اگر هندسه های پیچیده تری مدنظر است، لازم است از قالب هایی با هسته Side-Action یا دیگر اینسرت ها استفاده شود.
هسته های Side-Action المان های متحرکی هستند که از بالا یا پایین وارد قالب شده و ساخت قسمت های بیرون زده را امکان پذیر می کنند(برای مثال یک سوراخ و یا حفره. این هسته ها باید بهینه استفاده شوند چرا که موجب بالا رفتن هزینه می شوند. در قسمت بعدی توضیحات بیشتری در مورد اینگونه هسته ها می دهیم.
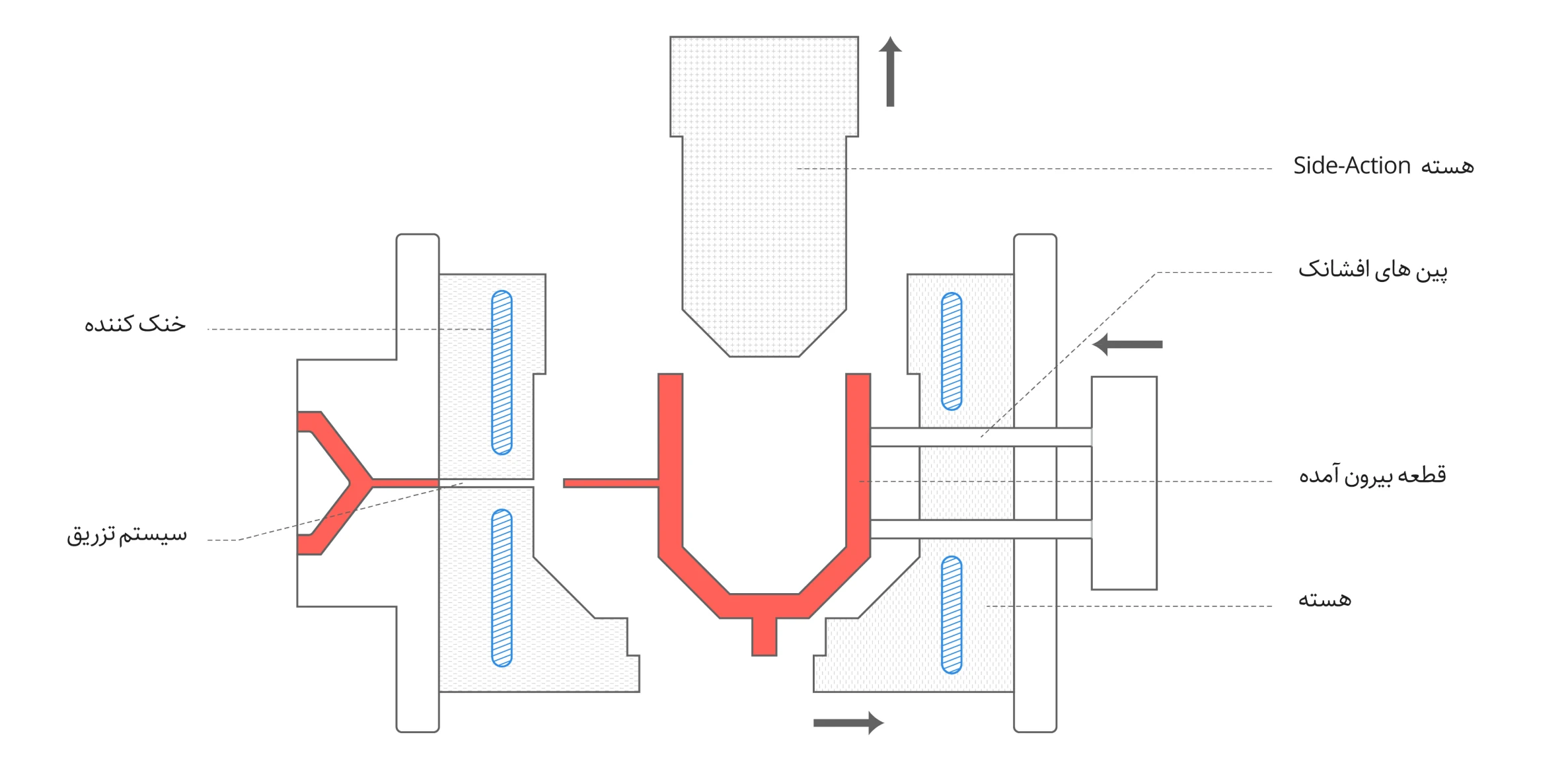
یک قالب با هسته های side-action در حین بیرون آوردن قطعه
دو قسمت یک قالب: ساید A و ساید B
قطعات تزریق پلاستیک دو طرف دارند: ساید A که مقابل حفره است (نیمه
جلویی قالب) و ساید B که مقابل هسته(نیمه پشتی قالب) است. این دو
قسمت معمولا کاربردهای متفاوتی دارند:
- قسمت A معمولا ویژگی های ظاهری بهتری داشته و قسمت Cosmetic نامیده می شود. سطوح قسمت A نرم بوده و بافتی متناسب با طراحی شما خواهند داشت.
- قسمت B معمولا شامل المان های سازی ای و پنهان قطعه (مثل ستون ها و…) می شود. به همین دلیل به این قسمت سایدِ کاربردی یا Functional می گویند. سایدِ B معمولا سطوح خشن تری دارد و جای پین های انژکتور روی آن دیده می شود.
تزریق ماده به درون قالب: سیستم تزریق
سیستم تزریق پلاستیک یا Runner System کانالی است که پلاستیک ذوب شده را به فضای خالی قالب هدایت می کند. این سیستم میزان جریان و فشار ورود پلاستیک مایع به درون قالب را کنترل می کند و پس از تزریق از قالب خارج می شود.
سیستم تزریق از سه بخش تشکیل شده است: حلقه تزریق (Sprue) ، گردنده سیستم تزریق (Runner) و ورودی (Gate).
- حلقه تزریق کانال اصلی است که پلاستیک ذوب شده هنگام ورود به قالب از آن عبور می کند.
- گردنده تزریق – runner – پلاستیک ذوب شده را روی صفحه ای که دو نیمه قالب به هم متصل می شوند توزیع کرده و حلقه تزریق – Spur – را به ورودی متصل می کند. هر قالب می تواند شامل یک یا چند تزریق کننده باشد. این رانر ها ماده اولیه را می توانند به سمت یک یا چند بخش قالب هدایت کنند.
- ورودی – gate – دروازه ورودی ماده به درون فضای خالی قالب است. هندسه و مکان گِیت از اهمیت زیادی برخوردار است. این ورودی تعیین کننده ی شیوه جریان یافتن پلاستیک درون قالب است.
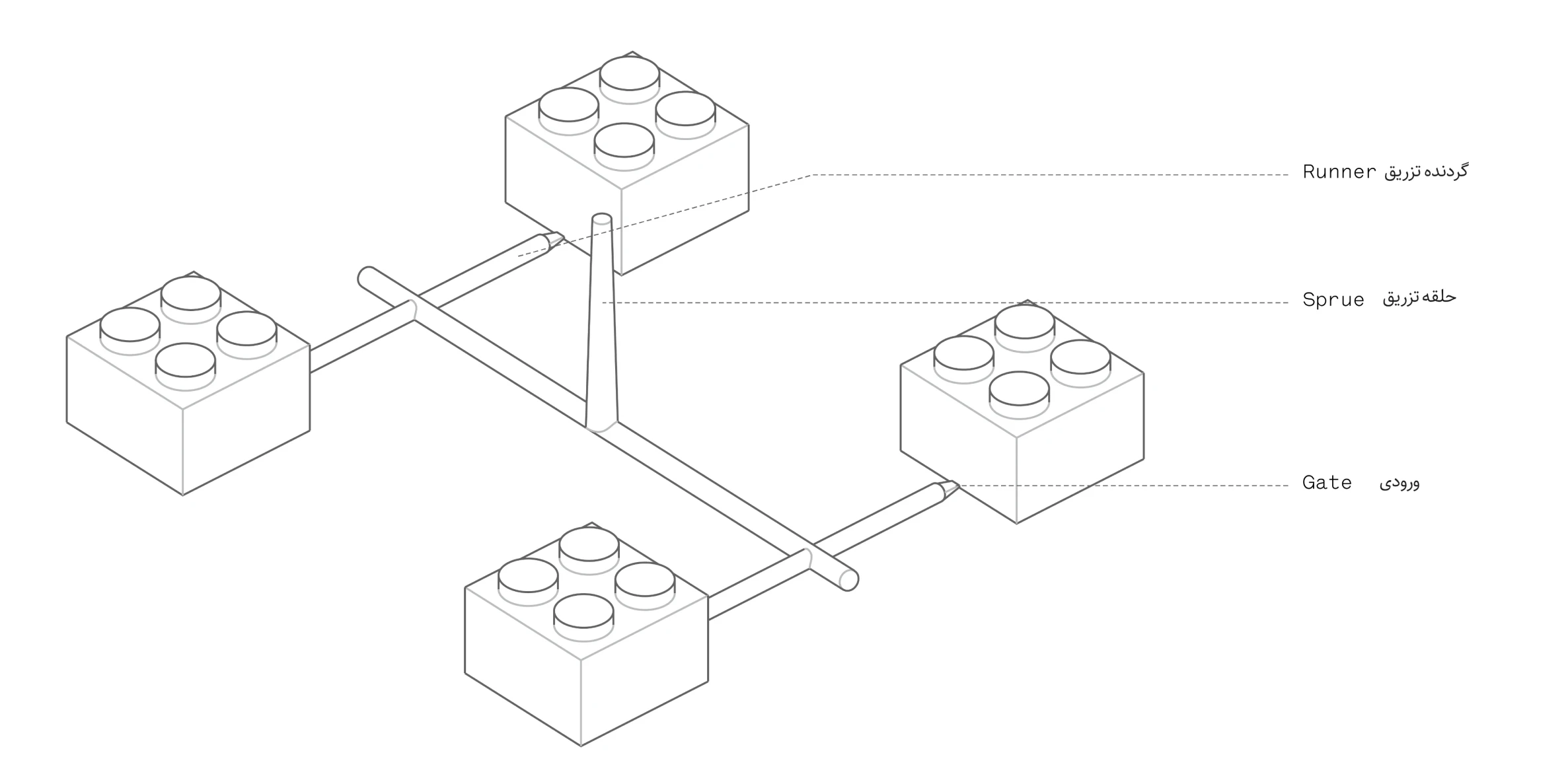
پلاستیک ذوب شده از حلقه تزریق به سمت گردنده تزریق جریان پیدا کرده و از طریق ورودی ها به قالب وارد می شود تا در هر نوبت تزریق پلاستیک چهار قطعه تولید شود.
در تزریق پلاستیک چهار نوع ورودی – گِیت – استفاده می شود:
- ورودی های کناری – Edge Gates : ورودیه های کناری پلاستیک را در نقاط اتصال بین دو نیمه قالب تزریق می کنند و پر استفاده ترین نوع ورودیه است. سیستم تزریق می تواند پس از پروسه به طور دستی حذف شود. روی قطعه در نقاط تزریق نقص های کوچکی دیده می شود که می توانند با پرداخت و پولیش اصلاح شوند.
- ورودی های تونلی – Tunnel Gates پلاستیک مایع را در زیر خط اتصال تزریق می کنند. سیستم تزریق این نوع از ورودیه ها به محض خروج قطعه از قالب به طور خودکار از قالب بیرون می آید و نیازی به حذف دستی آن نیست. این مسئله این نوع از ورودی ها را برای تزریق پلاستیک قطعات بزرگ بسیار مناسب می کند.
- ورودی سرقلم یا Hot tip به حلقه تزریق متصل است و پلاستیک را از بخش فوقانی قالب تزریق می کند. با این نوع ورودی تقریبا هیچ پلاستیکی به هدر نمی رود به همین دلیل برای تولید در تیراژ بالا سیستم های ایده آلی هستند. تنها مشکل اینگونه ورودی ها این است که یک گودی ریز روی قطعه در نقطه تزریق دیده می شود.
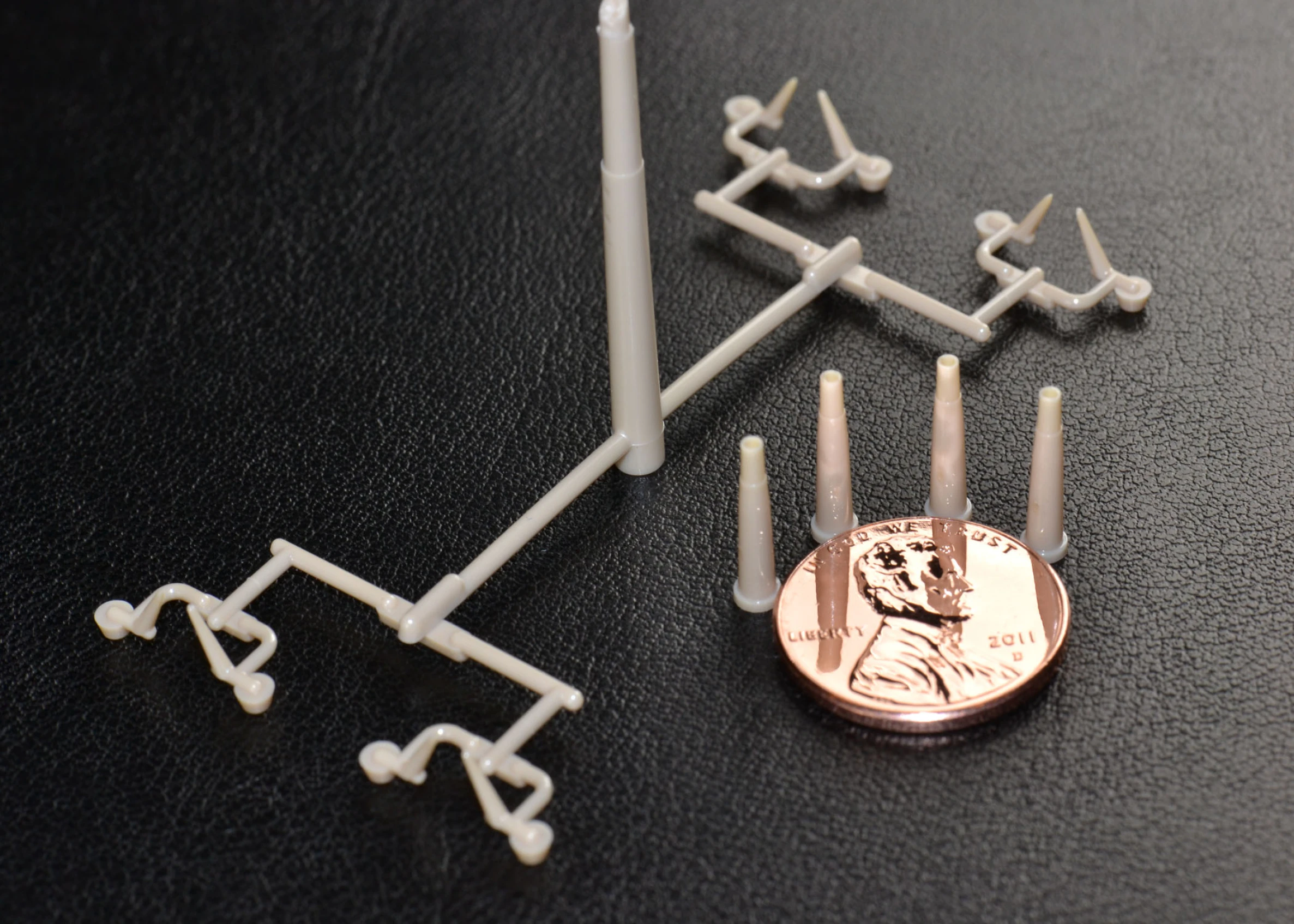
قطعه در کنار سیستم تزریق
تزریق پلاستیک آزادی زیادی در اختیار طراح می گذارد اما طبیعت این پروسه موجب محدودیت های خاصی می شود که شاید به طور عادی به ذهن طراح نرسد.
در ادامه لیستی از مهمترین نکات طراحی را آورده ایم که بهتر است هنگام طراحی برای تزریق پلاستیک یک قطعه آنها را رعایت کنید:
- تا جای ممکن ضخامت دیواره های مدل را یکسان درنظر بگیرید. دیواره هایی به ضخامت بین ۱.۲ تا ۳ میلیمتر برای کار با هر ماده اولیه ای مناسب هستند. اگر مقاطع شما ضخامت های مختلفی دارند تا حدی که طرح اجازه می دهد این تغییرات ضخامت را به طور پیوسته و نرم در قطعه ایجاد کنید. دستوراتی مثل Chamfer و Fillet برای ایجاد تغییرات نرم می توانند به شما در این کار کمک کنند. با این کار می توان از توزیع متناسب پلاستیک در کل فضای قالب اطمینان داشت.
- مقاطع ضخیم را توخالی کنید. مقاطع و دیواره های ضخیم می توانند مشکلات زیادی در پروسه تزریق پلاستیک ایجاد کنند. بهتر است این دیواره ها را توخالی درنظر گرفته و ضخامت استانداردی برای آن درنظر بگیرید. برای بالا بردن مقاومت این مقاطع می توانید در حجم توخالی تعدادی دنده و سازه های خرپا مانند درنظر بگیرید. با این روش تغییر شکل قطعه پس از خنک شدن آن به حداقل می رسد.
- برای همه دیواره های عمودی قطعه خود حدود ۲ درجه انحراف درنظر بگیرید.(Draft Angle) این انحراف خروج قطعه از قالب را ساده می کند. دیواره های عمودی که زاویه انحراف برای آنها درنظر گرفته نشده باشد روی سطوح خود اثرات سایش نشان می دهند.
- همه گوشه های قطعه خود را نرم کنید. برای نرم کردن گوشه های داخلی شعاعی در حدود نصف ضخامت دیواره درنظر بگیرید و برای گوشه های خارجی حدود ۱.۵ برابر ضخامت دیواره را درنظر بگیرید. با رعایت این نکته می توانید از پیوستگی ضخامت دیواره در تمام قطعه(حتی در گوشه ها) اطمینان داشته باشید.
در بخش های پیشین دیدیم که قالب Straight-pull می تواند برای تولید بیشتر هندسه ها با تزریق پلاستیک استفاده شود. اما برای تولید برخی قطعات پیچیده باید از هسته های Side-action استفاده کرد.
هسته های Side-action اینسرت هایی هستند که هنگام بستن قالب به صورت کشویی داخل آن رفته و پیش از باز کردن قالب از آن خارج می شوند. این هسته ها با مکانیزم کشویی از یکی از اضلاع قالب وارد شده و در جای خود قرار می گیرند (معمولا از ضلع فوقانی یا ضلع تهتانی). با این روش قطعات دارای بیرون زدگی و برآمدگی به راحتی قابل ساخت با تزریق پلاستیک هستند.
بهتر است هنگام طراحی هسته های Side-action به این نکات توجه کنید:
- باید فضایی برای ورود و خروج هسته از قالب وجود داشته باشد. این به این معناست که بیرون زدگی ها باید در بخش های خارجی قطعه باشند.
- هسته های Side-action باید به صورت قائم حرکت کنند. حرکت در زاویه ای به جز ۹۰درجه پیچیده تر بوده و هزینه و زمان ساخت را بالا می برد.
- برای هسته های Side-Action هم مانند دیگر قطعات حتما یک زاویه انحراف یا Draft Angle درنظر بگیرید.
وجود نقص های جزئی در قطعات تزریق پلاستیک امری طبیعی است.
برای مثال در محصولات خانگی که با تزریق پلاستیک ساخته می شوند معمولا جای خط اتصال بین دو قسمت قالب دیده می شود. اگر شکل ظاهری قطعه از اهمیت زیادی برخوردار است بهتر است این نقص ها با پولیش و پرداخت رفع شود و یا در مرحله طراحی قالب طوری درنظر گرفته شود.
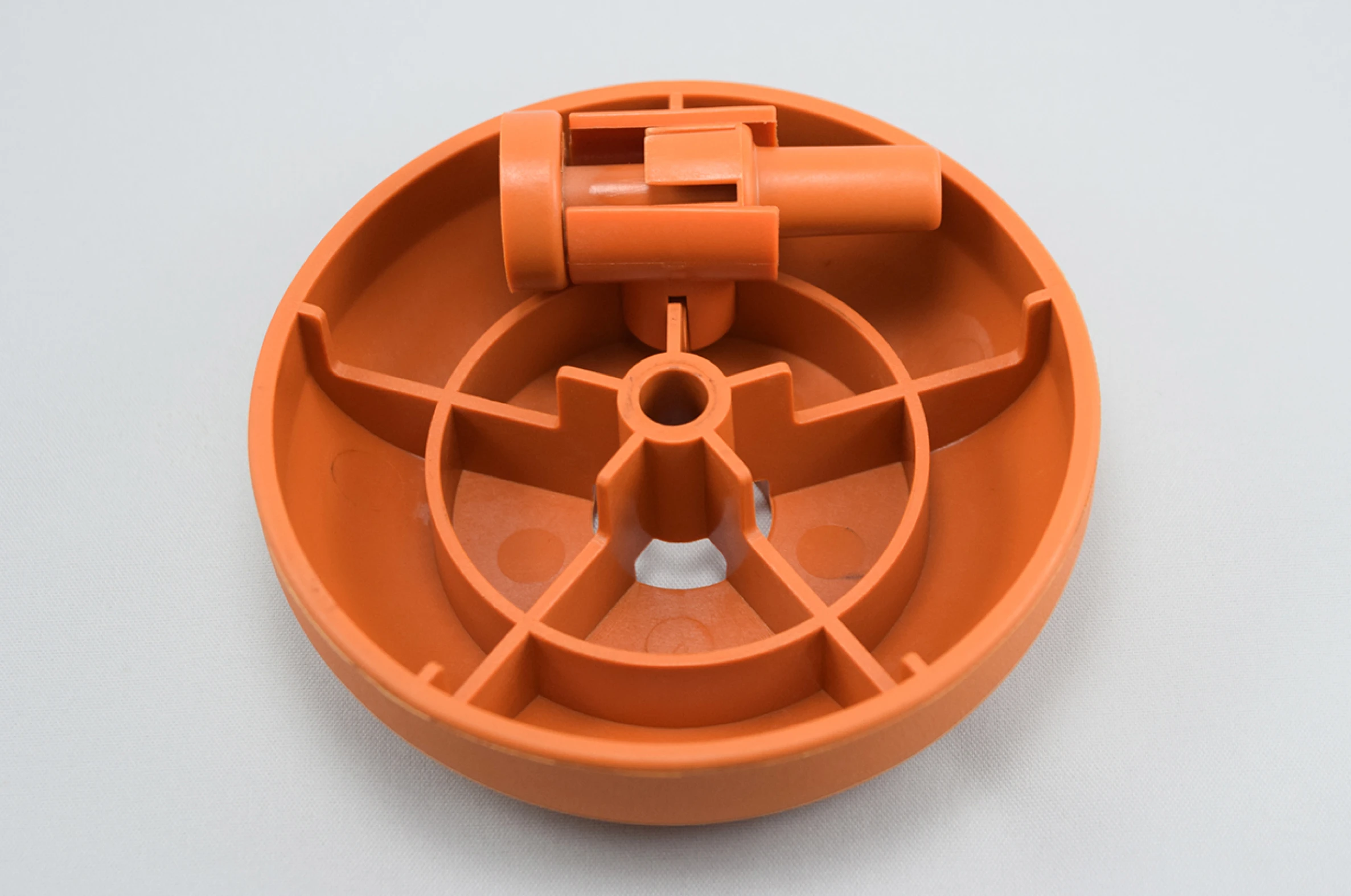
نیمه دوم تزریق پلاستیک یک قطعه کاربردی. دنده های درون این قطعه برای بالا بردن مقاومت آن در نظر گرفته شده است. جای پین های انژکتور در قطعه مشخص است.
نقص های جدی تر در تزریق پلاستیک وابسته به طراحی قالب و خواص مواد اولیه است. از آنجایی که هزینه ساخت قالب بالاست، طراحی صحیح آن از اهمیت زیادی برخوردار است. در ادامه یک لیست از معمول ترین مشکلات و توصیه هایی برای پیشگیری از آنها را آورده ایم:
تاب برداشتن:
پدیده تاب برداشتن قطعه در تزریق پلاستیک زمانی رخ می دهد که دمای
پلاستیک به طور ناهمسان پایین آمده و قطعه منقبض می شود. این مسئله
موجب خم شدن برخی جزئیات (یا کل قطعه) می شود.
- پدیده تاب برداشتن در تزریق پلاستیک در دیواره هایی با ضخامت های ناپیوسته، در گوشه های تیز و در مناطق بیش از حد ضخیم یا بیش از حد نازک بیشتر اتفاق می افتد. رعایت نکات بخش قبلی می تواند برای جلوگیری از تاب برداشتن قطعه به شما کمک کند.
تورفتگی یا پدیده Sinking:
تورفتگی زمانی رخ می دهد که میانه صفحه قطعه هنگام پایین آمدن دما
به سمت مرکز قطعه فرو می رود. این مشکل هم به دلیل تغییر دمای
ناهمسان اتفاق می افتد.
- مقاطع ضخیم تا حد زیادی مستعد ایجاد تورفتگی هستند. استفاده از دیواره های نازک یا توخالی کردن مقاطع ضخیم تا حد زیادی ریسک پدیده Sinking در تزریق پلاستیک را کاهش می دهند.
خطوط جوش:
وقتی دو یا چند جریان تزریق پلاستیک با هم برخورد می کنند ممکن است
به صورت ایده آل با هم ترکیب نشوند. در نقاط برخورد این جریان ها می
تواند پدیده هایی مثل تغییر شکل مقطعی، دورنگ شدن قطعه ایجاد شود.
این نقص ها زمانی اتفاق می افتند که:
۱- قطعه تعداد زیادی حفره داشته باشد
۲-قطعه دارای جزئیات زیادی باشد که جریان تزریق پلاستیک را قطع می کنند.
۳-پلاستیک ذوب شده از طریق چندین ورودی (Gate) به قالب تزریق می شود.
- برای پیشگیری از این مشکلات بهتر است تعداد حفره ها محدود شود و یا از ترکیبات پلاستیک چسبناک تر استفاده شود.
هنگام تزریق پلاستیک ممکن است در بخش های بن بست قطعه(قسمت هایی که از یک طرف بسته هستند) هوا گیر کند و فشار هوا از جریان پلاستیک به داخل قطعه جلوگیری کند. این مسئله باعث می شود برخی مناطق قطعه به طور کامل از پلاستیک فشرده پر نشود.
دمای این هوای محبوس در قطعه می تواند بالا رود و قسمت هایی از قطعه را بسوزاند.
- با افزودن حفره های هواکش در نقاط بحرانی می توان از ایجاد این مشکل پیشگیری کرد.
یکی از ویژگی های مثبت تزریق پلاستیک طیف گسترده پلاستیک های سازگار با این تکنولوژی است.بیشتر ترموپلاستیک ها می توانند تزریق پلاستیک شوند. ترموپلاستیک های استاندارد می توانند با افزودنی هایی مثل فیبر،ذرات لاستیک، مواد معدنی،مواد مقاوم در برابر آتش و دیگر ترموپلاستیک ها مقاوم شوند و خواص ویژه ای به دست آورند.
درنظر داشته باشید که هزینه ترموپلاستیک ها از ۷-۱۰ دلار برای هر کیلوگرم ABS و HDPE تا ۱۴۰ دلار به ازای هرکیلوگرم PEEK و PEI می تواند باشد.
در ادامه می توانید پر استفاده ترین مواد اولیه تزریق پلاستیک و خواص اصلی هرکدام را در جدول زیر ببینید:
مواد اولیه | خواص |
ABS |
کاربردها: محصولات مصرفی، محفظه ها |
Nylon (PA 6, 66 & 11) |
کاربرد ها: وسایل خودرو، چرخدنده ها |
HDPE |
کاربردها : محصولات مصرفی، قطعات پزشکی |
Delrin (POM) |
کاربردها: لوازم خانگی و قطعات مکانیکی |
Polycarbonate (PC) |
کاربردها: محصولات مصرفی، چراغ خودروها |
ABS/PC |
کاربردها: محفظه لوازم الکترونیکی، لوازم خودرو و… |
PEI (Ultem) |
کاربردها: صنعت هوافضا و محصولات پزشکی |
PEEK |
کاربردها: صنعت هوافضا، گاز و نفت |
Polystyrene (PS) |
کاربردها: لوازم خانه و بسته بندی |
Polypropylene (PP) |
کاربردها: مایعات و بسته بندی |
یک افزودنی بسیار پرکاربرد در بالا بردن سختی قطعات تزریق پلاستیک، فایبرگلاس است. فایبرگلاس می تواند در نسبت های ۱۰، ۱۵ یا ۳۰% برای رسیدن به خواص مکانیکی مختلف با ترموپلاستیک های ترکیب شود.
همچنین با افزودن رنگدانه ها به ترکیب متریال (نسبت نزدیک به ۳%) می توان قطعه را با هر ترکیب رنگی تولید کرد. رنگ های استاندارد تزریق پلاستیک عبارت اند از: قرمز، سبز، زرد، آبی، مشکی و سفید که می توانند با هم ترکیب شده و طیف گسترده ای از رنگ ها را پوشش دهند.
به طور معمول قطعاتی که با تزریق پلاستیک ساخته می شوند آماده استفاده هستند و عملیات پست پروسس محدود به حذف سیستم تزریق است. همچنین پس از تزریق پلاستیک می توان جزئیات بسیار دقیق را برای رسیدن به خطای پایین تر با ماشین کاری در قطعه ایجاد کرد.
قالب تزریق پلاستیک معمولا با ماشین CNC ساخته می شود. این قالب معمولا از آلومینیوم یا استیل ساخته شده و عملیات پست پروسس معمول می توانند روی آن پیاده شوند.
در ادامه یک لیست از روش های معمول پولیش، پرداخت و پست پروسس قالب های تزریق پلاستیک را در قالب جدول زیر آورده ایم:
فینیش | ویژگی ها |
ساده | خطوط حرکت ابزار روی سطح قطعه دیده می شود. نامناسب برای قطعات تزیینی. |
نرم شده | قالب سمباده زده شده و خطوط ابزار حذف می شوند. برخی خطوط سمباده کاری قابل مشاهده خواهند بود(بین ۱۰-۱۲ میکرون). |
پولیش | قالب ابتدا سمباده زده شده و با سوسپانسون الماس پولیش می
شود. فینیش آینه ای ( با Ra 1-2 میکرون). |
سند بلاست | جای ابزار از قطعه محو شده و یک بافت نرم روی سطوح قطعه تشکیل
می شود. فینیش مات مناسب برای محصولات زیبا |
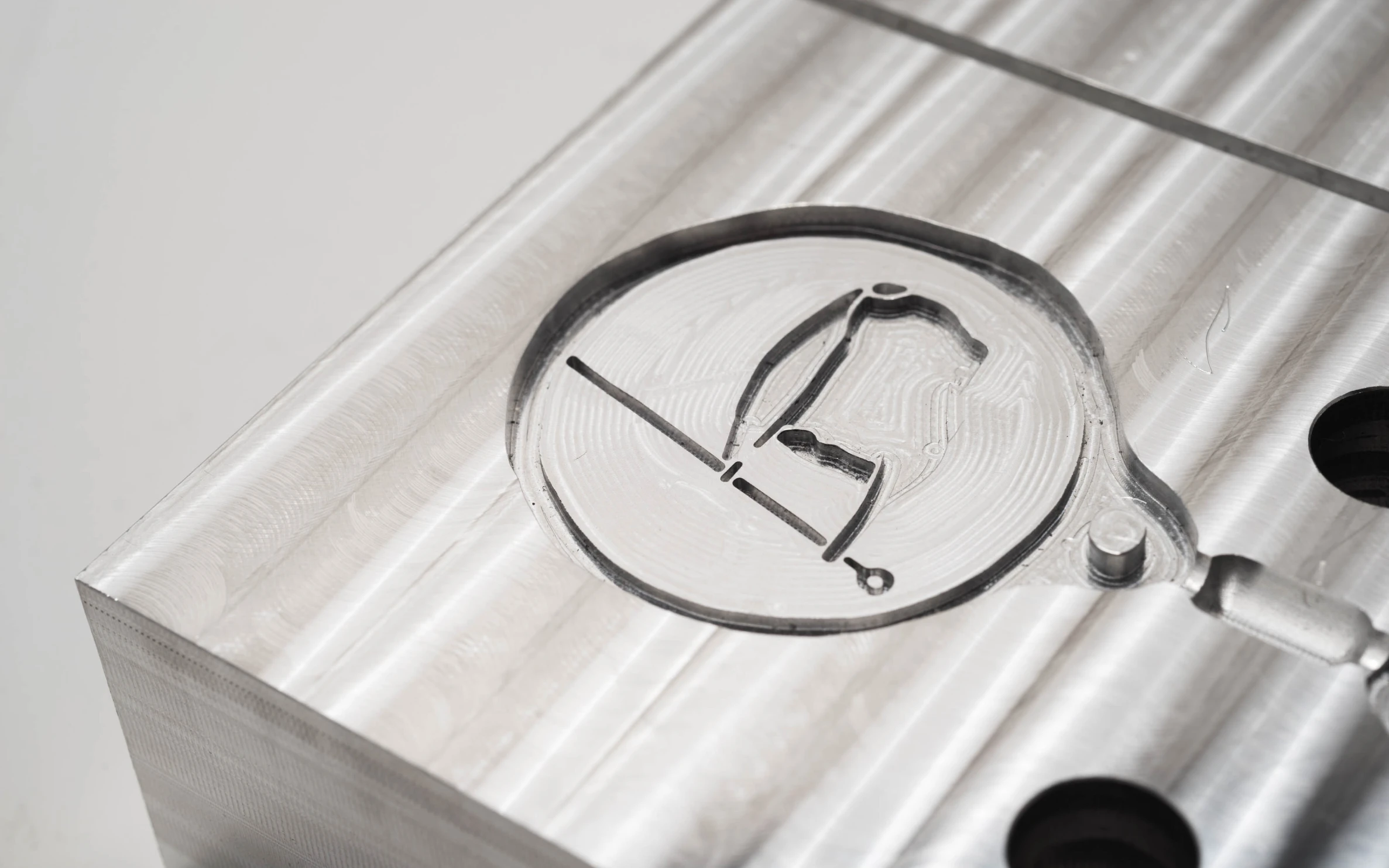
جزئیات یک قالب پولیش نشده به همراه تزریق کننده و ورودی(gate)
هزینه هر قطعه در تزریق پلاستیک می توانید با فرمول زیر حساب شود:
تعیین کننده اصلی هزینه تزریق پلاستیک، هزینه ماشین کاری و در واقع هزینه ساخت قالب است. از آنجایی که ساخت قالب برای هر تیراژ به صورت محدود انجام می شود طبیعی است که هر چه تیراژ بالاترباشد، هزینه ساخت به ازای هرقطعه پایین می آید.
هزینه مواد اولیه برای ساخت هر قطعه ثابت بوده و به نسبت هزینه پایینی است. هنگام اندازه گیری وزن مدل خود برای تخمین متریال مورد نیاز حتما سیستم تزریق را هم در نظر بگیرید.
هزینه های ساعتی عبارت اند از هزینه های ماشین و نیروی انسانی. این هزینه ها مستقیما وابسته به موقعیت جغرافیایی کارگاه تولید و ابعاد قطعه تولیدی هستند(قطعات بزرگتر نیاز به فشار هوای بالاتر و ماشین های گران تر دارند.).
به عنوان مثال:
فرض کنید که شما در حال طراحی یک قطعه بهینه برای تزریق پلاستیک هستید، این قطعه ابعاد ۲۰۰*۲۰۰*۴ میلیمتر داشته و وزن آن حدود ۵۰ گرم است.
برای یک قطعه با این ابعاد ، هزینه ساخت قالب حدود ۳۰۰۰۰دلار می شود. این قطعه یک ابزار خانگی است و هزینه مواد اولیه آن به نسبت پایین است. هزینه حدودی یک ترموپلاستیک مناسب – مثل ABS یا HDPE گرید بالا – حدود ۱۰دلار به ازای هر کیلوگرم است.
زمان چرخه تولید را می توان به طور متوسط ۸۰ ثانیه درنظر گرفت در نتیجه هر ساعت حدود ۴۵ قطعه تولید می شود. جمع هزینه ساعت کار ماشین و نیروی انسانی حدود ۳۰دلار است.
با در نظر گرفتن این فرضیات، گراف زیر در مورد هزینه تزریق پلاستیک هر قطعه در تیراژهای مختلف کشیده شده است:
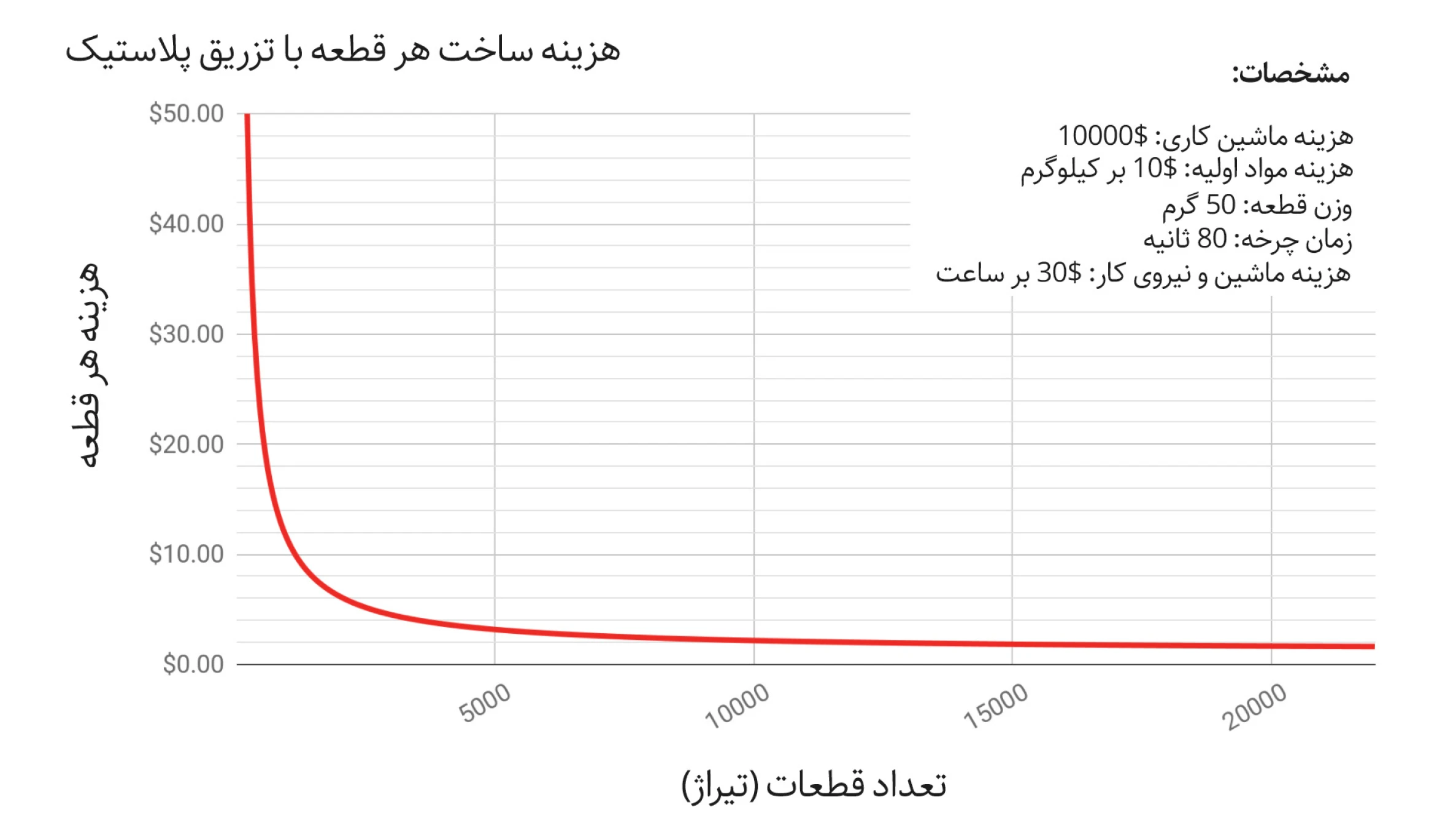
اطلاعات از 3DHubs
هزینه ساخت هر قطعه تا تیراژ ۵۰۰۰ به سرعت کاهش پیدا کرده و برای بالای ۲۰۰۰۰ قطعه به میزان ثابت حدود ۲دلار می رسد. برای حجم های پایین تر هزینه ساخت کاملا وابسته به هزینه ساخت قالب تزریق پلاستیک است. برای مثال اگر تیراژ تنها ۱۰۰۰ قطعه باشد هزینه ساخت هرکدام حدود ۳۰دلار می شود.
با ساده کردن طرح قطعه می توان از پیچیدگی قالب کاست و هزیه را تا حد قابل توجهی کاهش داد. این کاهش هزینه تزریق پلاستیک در تیراژهای پایین (بیش از ۱۰۰۰ قطعه) را به نسبت به صرفه می سازد.
از پرینت سه بعدی می توان برای ساخت قالب های تزریق پلاستیک تیراژ پایین استفاده کرد. با استفاده از پرینت سه بعدی در تزریق پلاستیک تا حد زیادی هزینه ساخت قالب پایین آمده و تولید قطعه با تیراژ پایین به صرفه می شود.
ضعف اساسی قالب های پرینت سه بعدی تزریق پلاستیک این است که پس از چند صد شات تزریق غیرقابل استفاده می شوند.
قابلیت ها و محدودیت های تکنولوژی تزریق پلاستیک در ادامه به طور خلاصه آورده شده است:
قابلیت ها:
- تزریق پلاستیک به صرفه ترین تکنولوژی برای تولید قطعات پلاستیکی یکسان در تیراژهای بالا است.
- طیف گسترده ای از مواد اولیه برای تزریق پلاستیک موجود است، خواص فیزیکی این مواد می توانند بسته به ملزومات طرح شما سفارشی سازی شوند.
- تزریق پلاستیک تکرارپذیری بالا را در کنار سرعت بالای تولید در اختیار تولیدکنندگان می گذارد(یک چرخه ساخت معمولا کمتر از ۶۰ثانیه طول می کشد.).
محدودیت ها:
- هزینه اولیه تزریق پلاستیک بسیار بالاست. این هزینه بالا باعث می شود که تزریق پلاستیک تنها برای تولید در تیراژ بالای ۱۰۰۰ قطعه مناسب باشد.
- اصلاحات در طرح پس از ساخت قالب می توانند بسیار هزینه بر باشند.
- زمان بین شروع پروسه و تحویل قطعه نسبت به دیگر تکنولوژی های
ساخت بالاتر است و می تواند از ۴ هفته تا چندین ماه طول بکشد.
این زمان به پیچیدگی قطعه و میزان تولید بستگی دارد.
اگر متن بالا را نخواندید:
- پیش از وارد شدن به پروسه تزریق پلاستیک، قطعات خود را با پرینت سه بعدی و یا ماشین کاری CNC نمونه سازی کرده و طرح خود را نهایی کنید.
- تعیین کننده اصلی هزینه تزریق پلاستیک، قالب آن است. هزینه ساخت قالب تزریق پلاستیک به هندسه قطعه بستگی دارد. هرچه قطعه ساده تر باشد، ساخت قالب آن ارزان تر خواهد بود.
- برای پیشگیری از نقص های احتمالی در قطعه، ضخامت دیواره ها را پیوسته طراحی کرده، برای دیواره های عمودی حتما حدود ۲ درجه زاویه انحراف درنظر بگیرید و همه گوشه های قطعه را نرم(Fillet یا Chamfer) درنظر بگیرید.
- تزریق پلاستیک برای تولید بیش از ۱۰۰۰ قطعه به صرفه است اما راه حل های دیگری مثل استفاده از پرینت سه بعدی برای ساخت قالب می تواند هزینه ساخت را به طرز قابل توجهی پایین بیاورند.